For over ten years, we’ve poured our hearts into crafting top-tier LED automotive lighting. We’re not just building lights; we’re building confidence on the road. That’s why we relentlessly test our products, discarding anything that doesn’t meet our exacting standards – and yours. We’ve spared no expense in our pursuit of excellence, constantly innovating and refining our designs to deliver universally compatible lights that are as reliable as they are bright.
Our five dedicated production lines are humming with cutting-edge technology, overseen by expert engineers at every step, from initial design to final quality check. Our seasoned procurement team, with over two decades of industry experience, sources only the finest components. And with 80% of our production staff boasting over five years of experience, meticulous craftsmanship is simply part of our DNA.
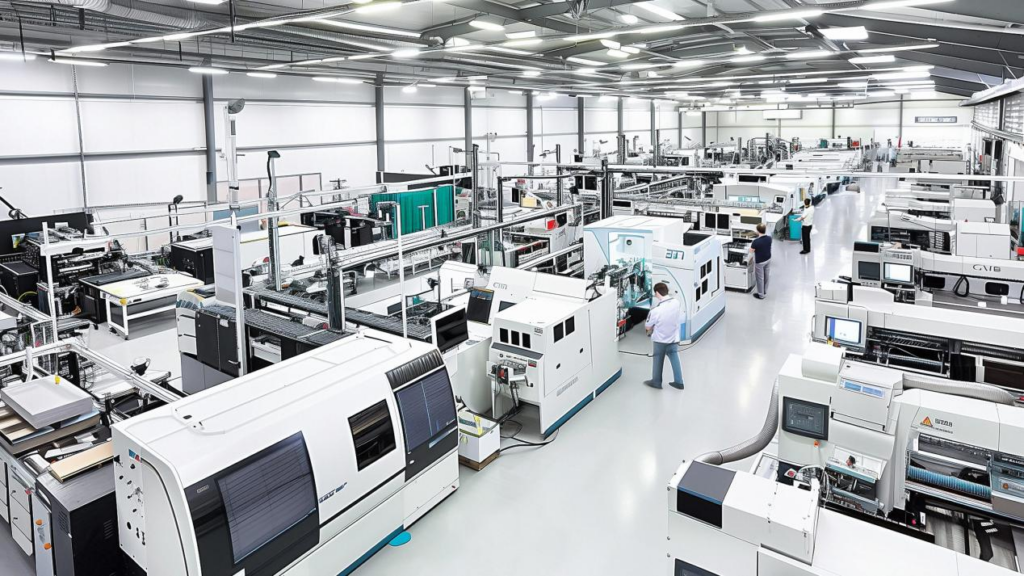
We start with premium 50mil LED chips, achieving a brilliant luminous efficacy of ≥130lm/W – that’s high brightness with low energy drain. These chips are precisely placed using automated die bonding machines and coated with a uniform layer of silicone and phosphor (color temperature deviation ≤ ±200K) for consistent color. We use ceramic substrates (24W/m·K thermal conductivity) for our driver boards, eliminating the risk of thermal expansion failures common with epoxy resin. Phosphor coating uniformity is held to within ≤5% to prevent color drift, and the whole assembly is baked and cured for maximum durability. The lamp housing is crafted from robust 6063-T5 aluminum alloy, striking the perfect balance between heat dissipation and strength. High-temperature silicone wiring (-60℃~200℃) prevents aging and short circuits, while our efficient LLC resonant circuit topology (>93% efficiency) minimizes power loss. Our lights are built to withstand the elements, meeting IP68 waterproof and dustproof standards, with silicone seals and ultrasonic welding ensuring a rock-solid barrier against the elements. We even put them through rigorous 20G vibration testing to simulate real-world road conditions and guarantee the integrity of every solder joint.
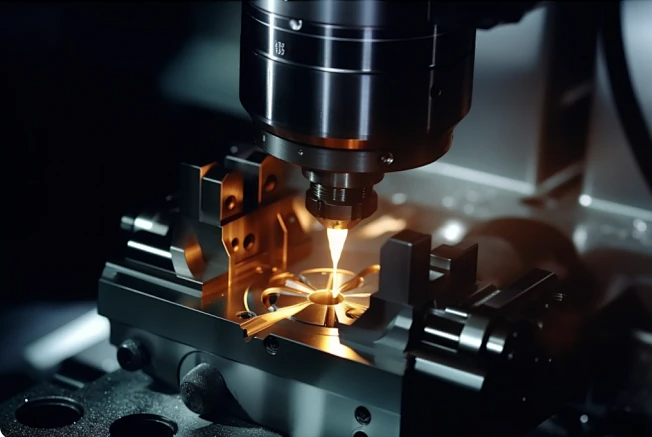
But our commitment doesn’t end when the lights leave the factory. We meticulously package each unit in anti-static aluminum foil bags with protective foam to prevent damage during shipping. Laser marking with batch numbers, production dates, and key parameters (like BIN codes) ensures full traceability throughout the product’s lifecycle. Because when it comes to your safety, we don’t just meet expectations – we exceed them.